How to Make Custom Hats: A Step-by-Step Guide from a Professional Manufacturer
Published On: July 11, 2025 By: chen hui
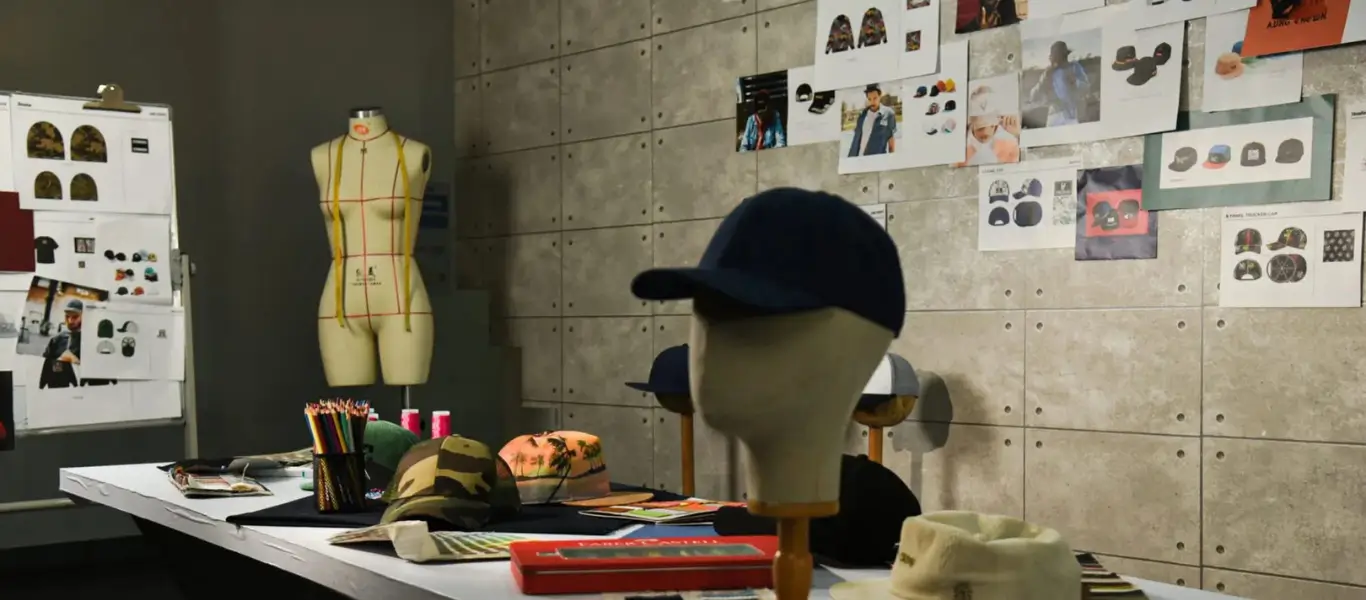
In this personalized consumption era, custom hats have become brand strategies, enterprise IP creations, and trendy designs. As a deep ploughing custom manufacturer of hats and clothing for over 26 years, Aung Crown processes more than 30+ custom designs per day, from functional hats for outdoor sports brands, limited-edition hats for trendy designers, gifts for enterprise celebrations, to co-branding with influencers. We have found that the point that can touch clients most is accurately communicating their demands and the excessive quality control for craftsmanship and details.
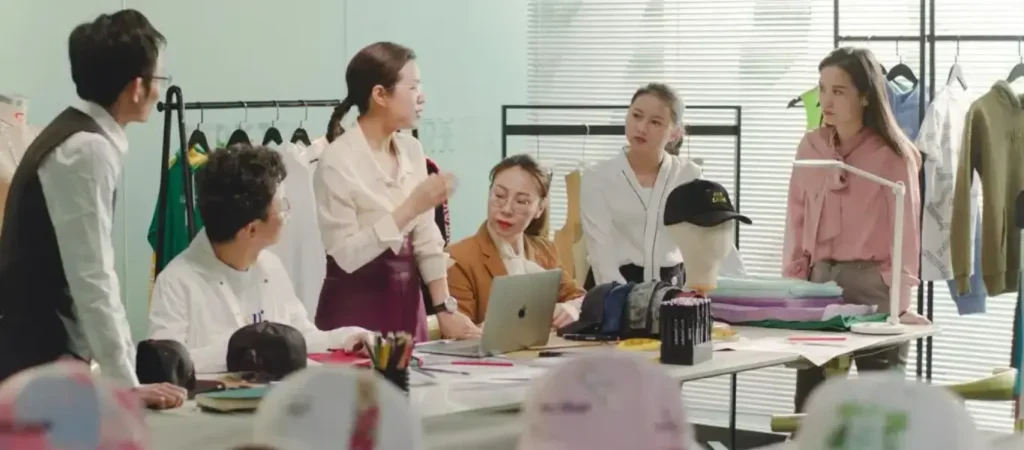
This blog is based on our actual production process that is divided into 6 core points to help people to get professional knowledge from a drawing to a real hat, and answers to frequently asked questions. All these aren’t from AI, and they are from our production experience and conclusion.
Step 01: Deeply Communicate the Demands
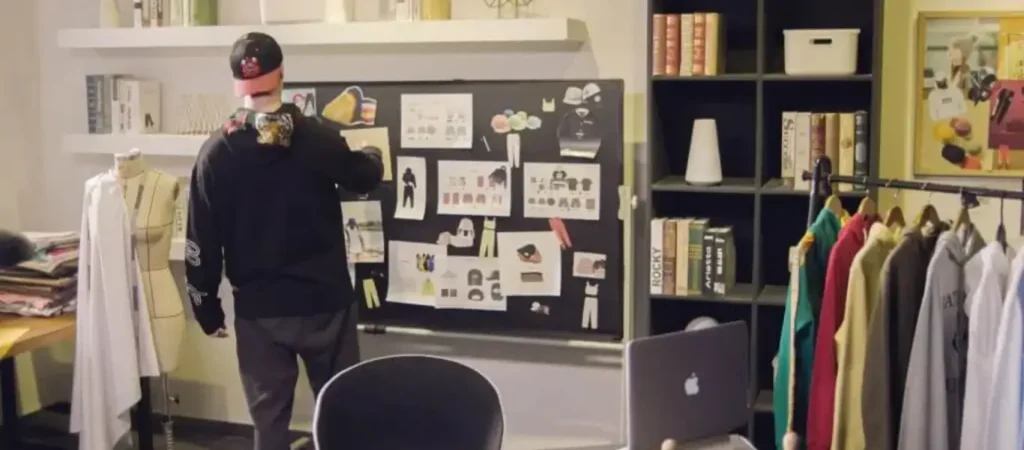
This is the beginning of custom hats, and it’s decided that 80% of the real hats are. In general, many clients think custom hats are equal to providing a designed draw + placing the order”. However, according to our production experience, 70% unsatisfied problems with custom hats are derived from insufficient communication. Therefore, our teams will check all the details through a detailed sheet of custom hats.
- Targeted Scenes: Lightweight and breathable feature for daily wear; Water-repellent and anti-UV properties for outdoor sports. Emphasizing logos for brand activities and special crafts for a limited-edition collection. Different scenes have different requirements for fabrics, hat structures, and crafts. For example, riding caps need inner sweat-wicking sweatbands and breathable mesh designs, and high-end top hats might need handmade hemming.
- Priority for Core Demands: Controlling cost, shortest turnaround time, or extreme craftsmanship? We had chosen 3D embroidery for our trendy clients with 15-day delay for the turnaround time. Also, lowered the cost previously for enterprise gifts through heat transfer printing. Our priority is decided by our clients’ core needs.
- Detailed Parameters: Head circumference – adults/kids; hat shapes: curved brim/flat brim/bucket hat; color hex code – Pantone color card confirmation; logo places: front/side/back panel or on the brim; crafts: embroidery/printing/hot stamping. The differences of all these parameters may lead to the final caps differing from the caps that the client initially wanted.
Tips: We always recommend that our clients offer a referring cap or even a competitive hat for us. Then we can use our professional machine to detect the weight of fabric, yarn density, and dimensional tolerance to make sure the custom hats are over 95% restoration.
Step 02:Design Proofing

Design proofing is the step where the design drawing becomes a real hat. After we get the demand sheet of our clients, our design team will finish the two key projects: 3D modeling and process simulation.
3D Modeling & Process Simulation
Our designers draw the graphic design through CoreIDRAW or Adobe Illustrator, using professional software (like CLO3D) for 3D modeling to simulate the effect of wearing the hat. For example, an embroidered logo on the curved brim might deform due to the anchor, and the software can alert earlier. Even the outlay of embroidered eyelets affects the whole strength, or not, which can also be adjusted through simulation.
Physical Proofing
Physical proofing, also called hard proofing, is the 0.1mm detailed war. After confirming our clients with graphic designs, we start physical proofing to test.
Fabric Matching: Navy on the design drawing shows different color effects under lights, which might be bluish or grayish. Therefore, it needs the color card to confirm before production.
Feasible Crafts: For example, some clients want hot stamping and embroidery on the brim. However, the layering of both crafts might cause cracking, and it needs to adjust the order of both crafts or replace them with other crafts.
Dimensional Tolerance: The dimensional tolerance control is within ±0.5cm/0.2inches. Otherwise, it can affect the comfort of wearing hats, which is a detail that many small factories are easy to ignore.
Our Example: One of our clients wanted to lengthen the brim to 2cm/0.79inches to improve sun protection. But, after physical proofing, a long brim can cause the center of gravity to lean forward. Finally, we solved this balanced problem by adjusting the arc of the brim and adding the elastic buckle at the back.
Step 03: Choices of Fabrics
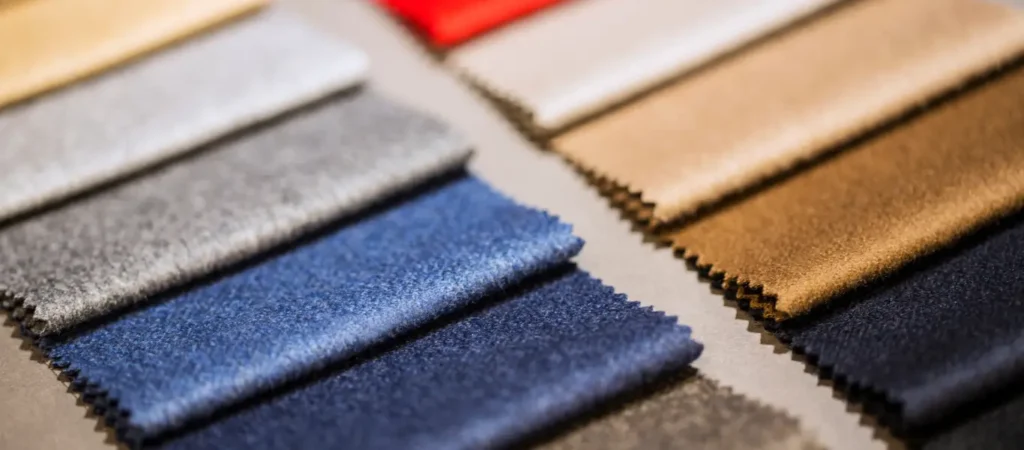
The knowledge of choosing fabric differs in different scenes. The soul of hats is the fabric. Here are the common fabrics that we use for custom hats.
Fabric Types | Properties | Suitable Scenes & Hats |
Pure Cotton/240-320g | Skin-friendly, breathable, moisture-wicking | Daily style and kids’ hats |
Polyester/180-260g | Quick-dry, wrinkle-resistant, climate-resistant | Outdoor sports and cargo caps |
Wool Blend/300g+ | Warm, stiff, and high-level texture | Fall/winter top hats and high-end customization |
Mesh Cloth/120-160g | Lightweight and excellently breathable | Running caps and baseball training caps |
Important experience:
- For dark-colored hats, it’s suggested to choose a pre-shrinking treatment to avoid shrinking and deforming after washing.
- For light-colored hats, it needs to check the colorfastness (National Standard ≥ Level 4); otherwise, sweat or friction might cause fading.
- Functional fabrics like UPF50+, antibacterial, and deodorizing, need to provide the third-party test reports to ensure compliance.
Step 04: Custom Hats Production
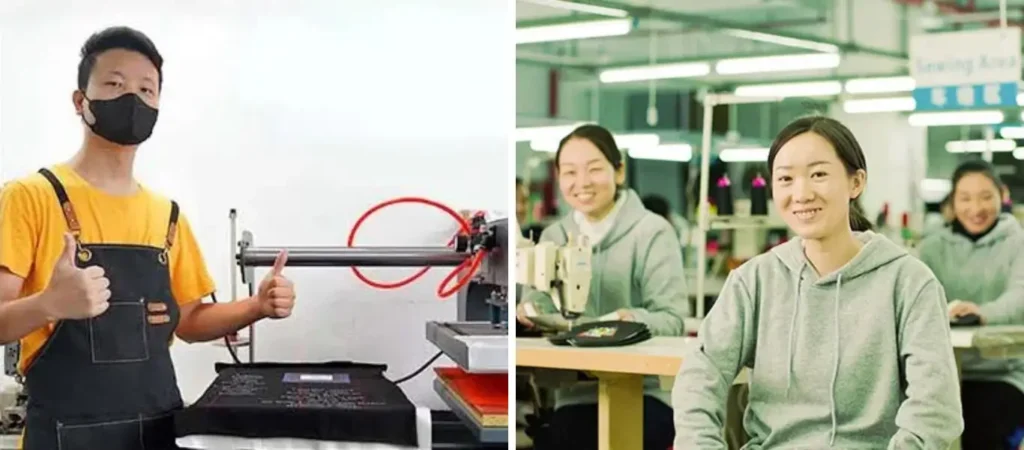
Each process is the exact fit between hands and machines. The hat production looks simple, but it includes 12 to 18 processes, even more (according to the complexity). Take common baseball caps as an example. Here are the main steps of the whole production process.
- Panel Cutting: Using auto cutting machines to cut fabrics and the dimensional tolerance ≤0.2mm/0.008inches (if the dimensional tolerance of panel cutting is up to 1mm/0.039inches, it can affect the sewing of panels.)
- Hemming: The hemming of hats is sewn with special hemming threads to avoid threads from breaking (common threads may break due to repeated bending).
- Sewing: Sewn by double needle sewing machines and the stitch density should be controlled at 12-14 stitches/inch(too sparse will not be durable, too dense will break easily).
- Structured Lining(Buckram): The structured front panel is inserted with a cardboard or a plastic sheet to become a structured hat or a buckram hat, to keep the front panel stiff and shaped.
- Logo Crafts:
- Embroidery: This stitch spacing is 0.3-0.5mm. Complex patterns require representation with different colored threads. For example, the gradient color needs to change threads at least 3 to 5 times.
- Heat Transfer: Here are the detailed parameters: temperature: 180℃-200℃/356℉-392℉; pressure: 8-10kg, time:15-20 seconds(the parameter deviation will cause the pattern to be blurry or break off.
- Hot Stamping: This needs special electric aluminum. If the temperature is too high, it will iron through the fabric. If the temperature is too low, the pattern won’t stick to the fabric for too long.
Step 05: Quality Inspection & Packing
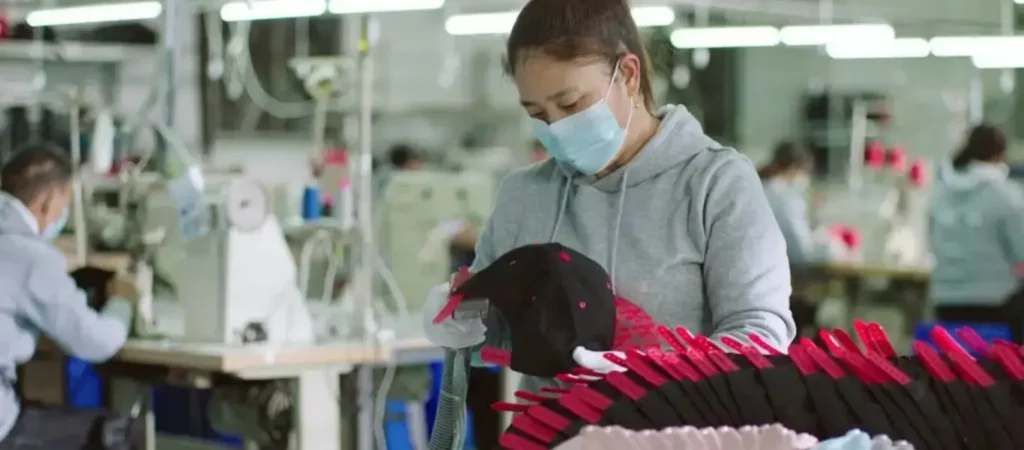
Zero flaw is our basic promise to our clients. Here are our 5 Inspection Processes for Defect Elimination
- Fabric Inspection: During the first step, our engineers will check the quality of materials such as fabrics, threads, and embellishments to ensure they meet the standards for the custom hats. Inspection items: Appearance, weight, density, feel, pattern, color, width, length, weft skew, and weft arc of the fabric. We use a four-point inspection method, and each yard of defects will be rated as four points for severe deficiencies. Example: All holes will be rated four points regardless of their diameter.
- Visual Inspection: During this step, our staff will inspect each custom-finished hat visually for any signs of defect in terms of stitching, embroidery, printing quality, and overall appearance. This helps identify any visible flaws that might compromise its quality and make for better customer experiences.
- Measurement Check: Following completion, each hat is measured against its specified requirements to ensure accurate dimensions such as brim width, crown height, head circumference, and any other essential measurements. Deviations from prescribed measurements are noted so correction may take place as necessary.
- Functionality Testing: Functional aspects of custom hats such as closures, adjustments, ventilation, and overall fit must be thoroughly tested to guarantee their intended use. This step involves testing components like buckles, straps, and closures to guarantee usability and comfort for each hat before shipping.
- Packaging and Labeling Inspection: Inspecting the labeling, branding, and packaging of custom-finished hats is the last step of production. We ensure that each product contains correct brand info, care instructions, as well as verified packaging that meets specified standards.
Packing
Packing is also an important step. Here are the common packing ways we use.
- General Order: OPP bag + cardboard box to prevent squeezing or pressing during shipping.
- High-end Custom Order: Moisture-proof paper + foam lining. Some clients want individual packing for each hat, and we will offer a service for designing custom packing boxes.
FAQ (Frequently Asked Questions)
Q: What’s the MOQ ( Minimum Order Quantity)?
A: For beanies: 50 pieces per style/color/size.For all other hats: 25 pieces per style/color/size. For all other clothing items: 100 pieces per style/color/size.
Q: What’s the turnaround time?
A: Common styles (embroidered logo + basic fabric) need 15 to 20 days. Complex styles (3D embroidered logo + special fabric) need 25 to 30 days. For rush orders, the turnaround time can be shortened to 5 to 7 days with a 10% extra fee.
Q: How to avoid “wrong proofing”?
A: Please be sure to confirm the “sealed sample” (the sample hat signed by both parties). The finished product must be completely consistent with the “color, process, and size” of the sealed sample; a “Quality Inspection Report” is required upon receipt, including data on color difference, color fastness, size tolerance, etc.
Conclusion
The essence of custom hats is to make sure that all the needs of our clients can be achieved in the end. Since 1998, Aung Crown has served more than 30,000 clients worldwide, and we still believe that custom hats are not produced 100% by drawings, but we use our expertise to help our clients optimize or revise their demands or projects. No matter whether we adjust the fabric weight to make hats lightweight or change the craft to lower the cost, our goal is to let our clients get their hats that can convey their brand spirits and positions.
If you have needs for custom hats, please contact us without hesitation. We offer a one-stop service from the beginning to the end.
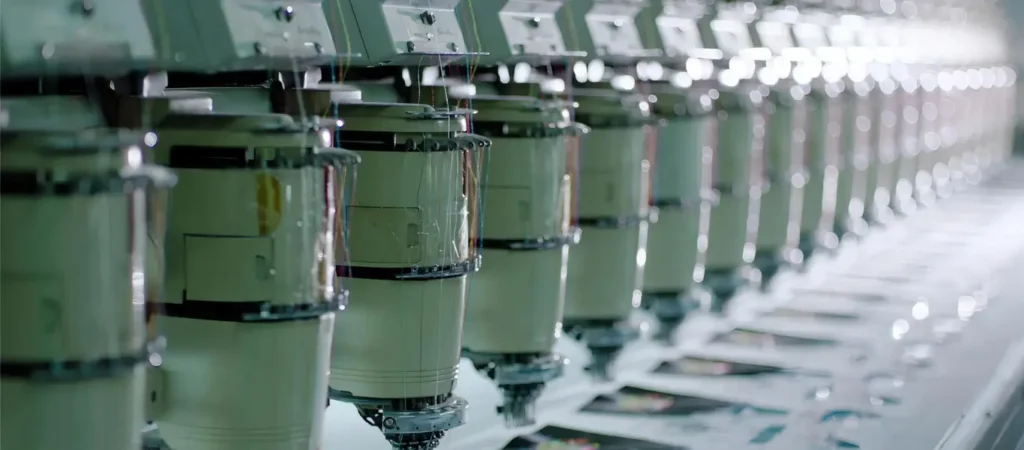