The Art of Snapback Cap Printing: Techniques and Methods
Published On: November 27, 2023 By: kailyn

Snapback caps have become a popular fashion accessory, allowing individuals to showcase their unique style and personality. One of the key elements that make snapbacks truly stand out is the art of snapback cap printing. Printing techniques are crucial in creating visually appealing and customised snapback caps, whether it’s a vibrant logo, a captivating design, or a personalized message.
Aung Crown is a leading hat maker that lets you customize your caps to your liking. For instance, their stylish unisex snapback cap is designed for comfort and versatility.
It is a size of 58cm and is a perfect fit for most individuals. The logo is expertly crafted using a combination of screen printing and flat embroidery techniques. Featuring a flat brim and five panels, this cap is made from high-quality cotton twill and acrylic materials for durability and style as you customize the cap to your requirements.
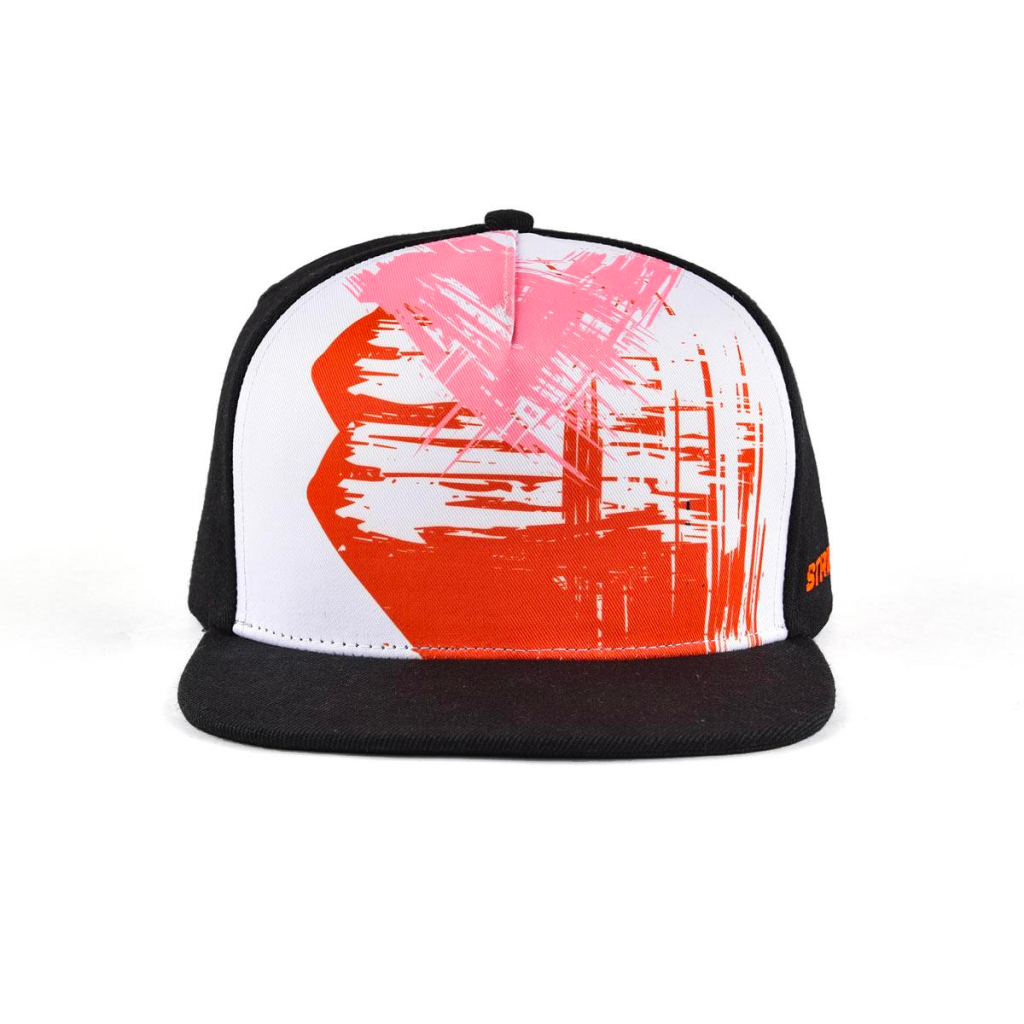
Importance of Printing in Snapback Cap Printing
Printing is a crucial aspect of snapback cap design as it allows for customization, branding, and personalization. The choice of printing technique can greatly impact the final appearance, durability, and quality of the printed design.
A well-executed print can transform a plain snapback cap into a striking fashion accessory. With the rise of custom cap printing, individuals and businesses have the opportunity to express their unique identity and create a lasting impression through their cap designs.
Types of Snapback Cap Printing Techniques
Screen Printing: Traditional and Versatile
Screen printing is a widely used technique for snapback cap printing. It involves transferring ink through a mesh screen onto the cap’s fabric. This technique offers versatility in terms of colors, textures, and effects. Screen printing is known for its durability, providing long-lasting prints that can withstand regular wear and washing.
It is suitable for both simple designs and intricate artwork, making it a popular choice among manufacturers and custom cap printers. The process has become more efficient with advancements in screen printing technology, allowing for higher production volumes and faster turnaround times.
Embroidery: Classic and Textured
Embroidery is a timeless technique that involves stitching the design directly onto the cap’s fabric. It offers a textured and three-dimensional effect, adding depth and richness to the design. Embroidery is often used for logos, monograms, and intricate patterns.
This technique provides a premium look and enhances the perceived value of the cap. With computerized embroidery machines, intricate designs can be created with precision and speed. The choice of thread colors and stitch types allows for customization and the ability to create captivating and intricate designs.
Heat Transfer: Vibrant and Detailed
Heat transfer printing involves using heat to transfer the design onto the cap’s fabric. This technique allows for vibrant colors, fine details, and intricate patterns. It involves printing the design onto a special transfer paper or vinyl and then applying heat to transfer the design onto the cap.
Heat transfer is especially suitable for gradients, photographs, and complex artwork designs. It offers a high level of customization and can be cost-effective for smaller production runs. With advancements in heat transfer technology, such as the use of eco-friendly and non-toxic inks, this technique has become more sustainable and environmentally friendly.
Sublimation Printing: Seamless and Full-Color
Sublimation printing involves transferring ink onto the cap’s fabric using heat and pressure. The design is first printed onto a special sublimation paper, and then the ink is heat-pressed into the fabric, resulting in a permanent, full-color, and seamless print.
Sublimation printing allows for vibrant colors, intricate designs, and unlimited creativity. It is particularly suitable for all-over prints and designs that require a high level of detail. With the advancement of sublimation technology, cap manufacturers and custom cap printers can now produce high-quality and durable sublimated snapback caps.
Factors to Consider
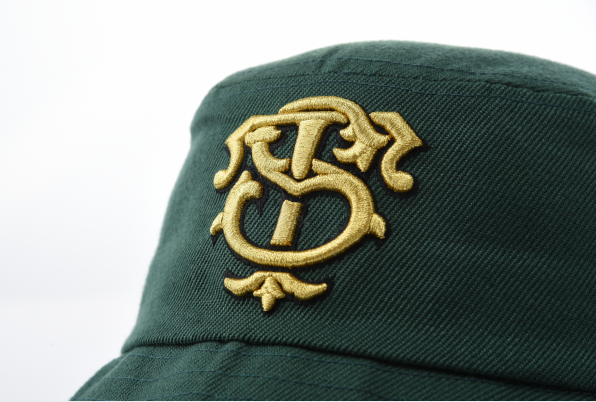
Cap Material Selection:
The choice of cap material greatly influences the printing technique and the final result. Different materials, such as cotton, polyester, and blends, require specific printing methods.
For example, screen printing is suitable for cotton caps, while heat transfer and sublimation printing work well on polyester caps. Understanding the characteristics of various cap materials is essential for achieving optimal printing results.
Design Placement and Size:
Determining the placement and size of the design is crucial for creating visually appealing snapback caps. Factors to consider include the cap’s panel layout, brim size, and available printing areas.
Balancing the design’s visibility, proportion, and aesthetic appeal is important to ensure that it stands out without overwhelming the cap’s overall look.
Color Matching and Accuracy:
Achieving accurate color matching is essential in snapback cap printing. The choice of printing technique, color profiles, and color calibration plays a significant role in ensuring consistent and accurate color reproduction.
Using standardized color systems, such as Pantone, helps maintain color consistency across different printing runs and materials.
Durability and Washability
The durability and washability of printed snapback caps are essential factors to consider. High-quality inks, proper curing methods, and adherence to recommended washing instructions contribute to the longevity of the print.
Ensuring that the print remains vibrant, sharp, and intact after multiple washes is crucial for customer satisfaction.
Step-by-Step Guide to Successful Snapback Cap Printing
Preparing the Artwork
Begin by creating or obtaining a high-resolution digital file of the desired design. Consider factors such as color separations, print sizes, and any additional effects or textures required. Ensure that the artwork is formatted appropriately for the chosen printing technique.
Cap Preparation
Properly prepare the snapback caps for printing by ensuring they are clean, free from dust or debris, and properly aligned. This step helps in achieving accurate design placement and enhances the adhesion of the ink or thread to the cap’s fabric.
Printing Process
Follow the specific instructions and requirements of the chosen printing technique. Whether it’s screen printing, embroidery, heat transfer, or sublimation, carefully apply the design to the cap using the recommended tools, machinery, and techniques.
Quality Control and Finishing
Conduct thorough quality control checks to ensure the prints meet the desired standards. Inspect for any inconsistencies, color variations, or defects. Once satisfied, finish the caps by trimming excess threads, heat-pressing to set the ink, or applying additional embellishments or finishes.
The Latest Innovations and Trends
Digital Snapback Cap Printing
Digital printing technologies have revolutionized the snapback cap printing industry. Direct-to-garment (DTG) printing allows for intricate, high-resolution prints with unlimited colors.
The ability to print-on-demand and produce small quantities without the need for screens or setup costs has made digital printing increasingly popular among custom cap printers.
Eco-Friendly Printing
Eco-friendly printing practices, such as water-based inks and recycled materials, have gained significant momentum in the industry. A study found that by using water-based inks instead of traditional solvent-based inks, cap printers can reduce VOC emissions by up to 90%.
Sustainability and eco-consciousness are growing trends in the printing industry. Many cap manufacturers and printers are adopting eco-friendly practices, such as using water-based inks, eco-solvent inks, and recycled materials. These innovations reduce the environmental impact of cap printing while maintaining high-quality results.
3D Printing
3D printing technology has opened up new possibilities in cap customization. With 3D printing, intricate and unique designs can be created, adding texture, depth, and dimension to snapback caps. This technology allows for producing one-of-a-kind caps with intricate patterns, logos, and textures.
3D printing has revolutionized the cap customization landscape. The global 3D printing market for the fashion industry is projected to reach $3.56 billion by 2024, with headwear being one of the key segments driving this growth.
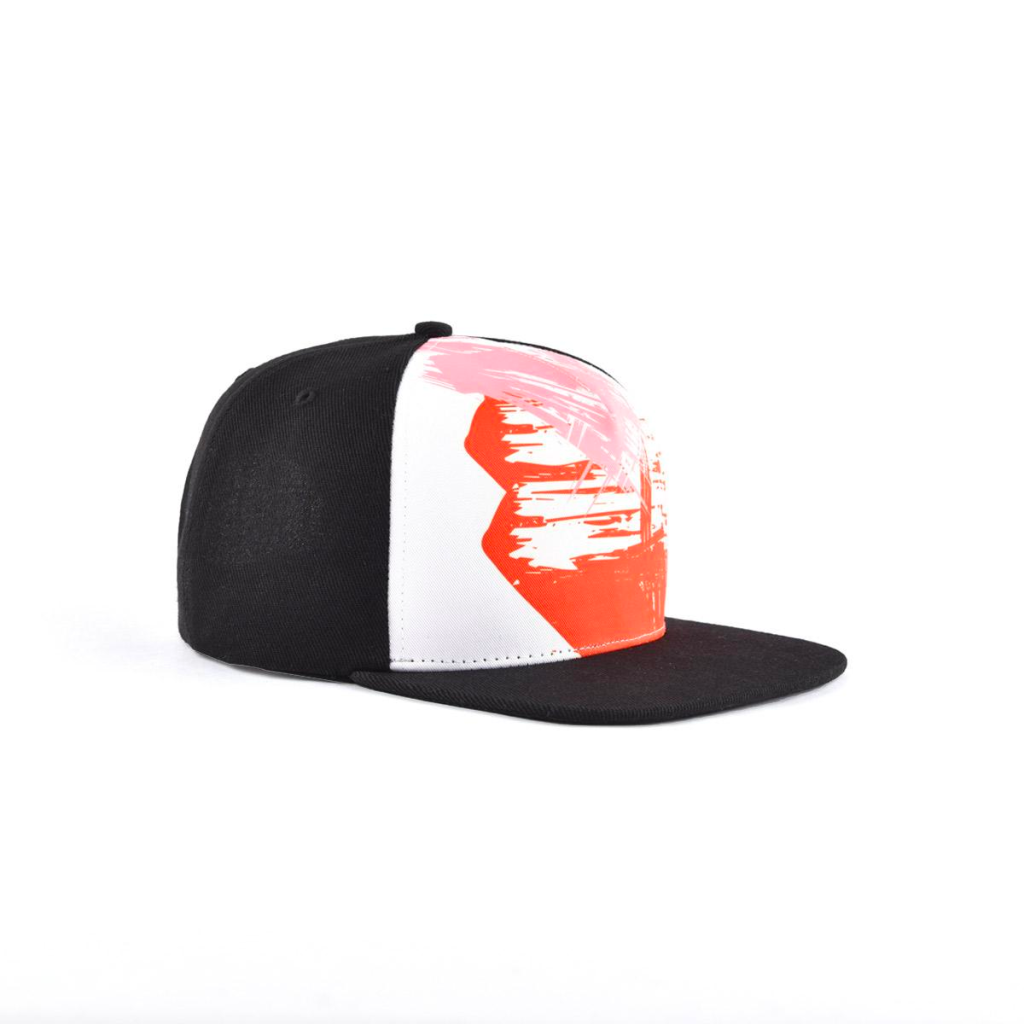
Conclusion
The art of snapback cap printing is a combination of creativity, technology, and skill. With a variety of printing techniques available, cap makers and custom cap printers have the means to create unique and eye-catching designs. The choice of printing technique depends on factors such as design complexity, desired effects, cap material, and production volume.
By understanding the different printing techniques, considering important factors, and staying updated on the latest innovations, cap printers can produce high-quality, durable, and visually appealing snapback caps. As fashion trends continue to evolve, the art of snapback cap printing will remain an integral part of the fashion industry, allowing individuals to express their personal style and make a statement with their headwear.